過酷な労働環境改善と効率化を考慮して、生産性と働きやすさを高める方法!!
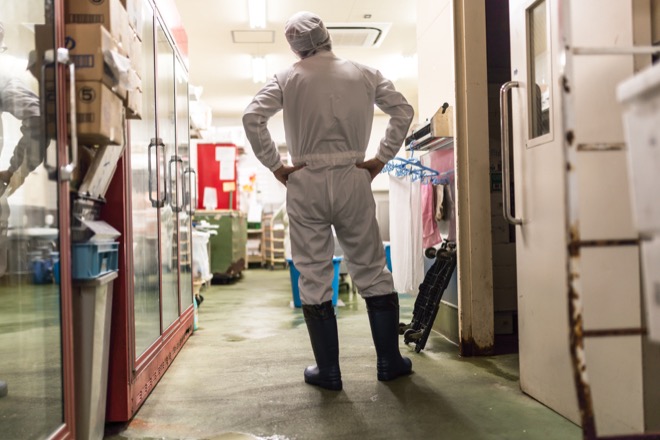
はじめに
食品製造業、飲食店で人手不足に悩まされている方も多いかと思います。産業構造が変わりITやサービスなどオフィス系の仕事が増える中で、食品関連産業は相対的に3K産業になっています。さらに給料が安い、不規則&長時間労働であるため更に嫌遠されがちです。
この厳しい環境で、さらに働く人のウィルビーイングの向上も要求されます。ウィルビーイングとは精神的、肉体的、社会的に満たされている状態の事を指します。
インフラとしての側面がある食品関連産業は深夜早朝、カレンダー通り休めない事や高い賃金を支払う事が難しい面が有ります。その中で3M(ムリ・ムダ・ムラ)を解消することは生産性を向上させるだけなく、働く人のウィルビーイングを向上させることは可能だと考えています。
カイゼンの順序はムリ→ムダ→ムラ
ムリ・ムダ・ムラは「3M」と呼ばれこれを削減することで生産性を向上させるという話は皆さんよく目にすることだと思います。
この「3M」に関しては3つのMの順番にいろいろと意見が有りまして「ダラリ」で覚えて、生産性を下げる順番として一番大きいのはムダ→ムラ→ムリで、ムダの解消を優先的におこなおう!というものです。
それは全くその通りで、カイゼン活動が定着して生産性の高い現場では遂行可能です。カイゼン活動が十分におこなわれていない会社で、いきなりムリからカイゼン活動を始めると現場からの反発が多くて協力が得られづらくカイゼンが進むのには大きな労力がかかります。
そこでムリの解消からカイゼン活動を始める事を私は勧めています。ムリの解消は生産性の向上には直接寄与する部分は少ないですが、現場担当者・作業者のメリットに直結し協力を得られやすいからです。
よって、私はムリ→ムダ→ムラの順番で「3M」を読んでいます。
「ムリ」のカイゼンについて
ムリは「痛い」「キツイ」「危険」「怖い」「悩む」「疲れる」「難しい」などの要素を持つ作業や工程です。労働集約型の食品製造業においては疲労が人の生産性や正確性を下げてしまいます。安全や労働災害にも直結しますし、長期疲労は従業員の出勤率の低下、離職につながります。
このムリの解消は作業者にとってもメリットが有りますので、カイゼン活動に前向きに取り組んでくれる場合が多いです。直接的な効果は見えにくいですが離職や出勤率、心理的安全性を向上させます。
「ムダ」のカイゼンについて
この様なムリのカイゼン活動が進み、活動を定着させた後にムダのカイゼンに切り込んでいきます。ムダの見つけ方はトヨタ生産方式の「7つのムダ」が有名で
「加工(作業そのもの)のムダ」
「在庫のムダ」
「作りすぎのムダ」
「手待ちのムダ」
「動作のムダ」
「運搬のムダ」
「不良を作るムダ」
(さらにムダをムダと思わないムダ、ニーズのミスマッチのムダも挙げられます)
この中の「ムリな動作」と「ムダな動作」からカイゼンしていきます。
ムダの削減で注意したい点が有ります。
機械や電子などほかの製造業の生産性向上を指導されている方が食品製造業に介入した場合、食品の特性や衛生に精通していないとカイゼンにより菌の増殖、アレルギーのコンタミなど「不良を作るムダ」へつながってしまう恐れがあります。
特に、「運搬のムダ」に関しては理由が有って運搬しているケースが有ります。食品は衛生度によってゾーニングをおこない、然るべき場所への移動はムダでは有りません。
加えて食品は製品の環境を変えることによって加熱・冷却・冷凍・乾燥などの加工工程となる、あるいは品温管理をおこなうことがあり、これも運搬が必要になります。アレルギーのコンタミや洗剤、殺菌剤の混入、菌の汚染を避けるため運搬が発生してしまいます。
「運搬のムダ」の解消には品質管理担当者と連携しておこなう必要が有ります。アカネサスの専門家は食品に特化していますので、その点は安心して任せる事ができますね。
さて、ムダは削減すべきものです。が、
一方でどんどん増やすべきムダが有りますが、どれだか判りますでしょうか?
正解は「手待ちのムダ」です。
「動作のムダ」などが削減されると生産性が向上して直接作業員の手待ちが増えていきます。手待ちが増えれば前後の工程を連結させて省人化することが可能になります。
またHACCPではいろいろな記録を保存する作業が有りますが、この手待ち時間を有効活用し記録、衛生や品質向上、次のカイゼンのための人と時間的な資源としていきます。
ムダのカイゼンが進むといよいよ「ムラ」のカイゼンに取り組みます。
「ムラ」のカイゼンについて
一部のムダはムラが大きいと発生します。このタイプのムダはムラ→ムリ→ムダの順番で発生します。
ムラ&ムリに対応するために各部門でクッション在庫が必要となり「在庫を作るムダ」「作りすぎのムダ」「加工(作業そのもの)のムダ」が発生してしまいます。
ムラのカイゼンには販売側と製造側それぞれの部分最適→会社全体の生産性が高くなる全体最適となるカイゼンが必要となります。製造側内部でも各部門で人員がおこなき来して助け合うような多能工の育成と体制の構築が必要になります。
そのためには、この対立を解消するトップダウンの強いリーダーシップが不可欠となります。
そうは言っても食品の特性上、どうしてもムラが出てきます。それは食品の旬の時期と市場で大量に消費されるイベントに需給と時間のギャップが発生するためです。これに対応するためには販売部門、製造部門との連携が不可欠になります。
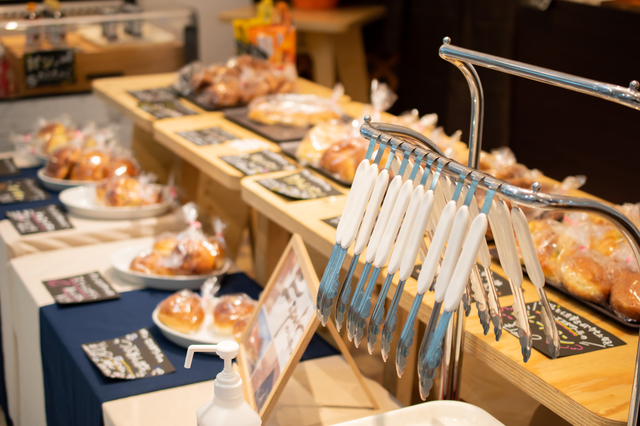
販売部門でのムラへカイゼン
売上至上主義からお客さんのニーズ(発注量・規格・品質・納期・タイミングなど)をつかむことを高く評価するように変容することが挙げられます。特にNGなのが「月末や上下期末にお客様にどれだけ売り込めるかが腕の見せ所」と考えている場合は、ねじ込まれたお客さんが在庫を抱える事になり次の発注への新しいムラが発生します。
経営者としても売上にノルマを課したい気持ちも有ります。そこに評価基準が偏ると、売れないノルマの販売予算で製造を依頼する→在庫になり賞味期限切れ。不良在庫になり責められることを恐れて過小な製造計画→上振れして増産依頼で現場は残業でコスト高となります。お客様と十分な対話をおこない、ニーズをしっかりと掴む仕組みを構築していきます。
トヨタ生産方式の特徴であるジャストインタイムを成立させるには販売予測が重要となります。販売予測を営業担当者の経験ではなく、「視える化」をおこないます。
詳しくはほかの専門家にお譲りしますが基本的には
- 昨対(昨年対比、昨月対比、昨週対比)の比較で増減の傾向を見る。
- 各商品の出荷棒グラフを作り、適切な移動平均線を重ねて増減の傾向を把握する。
- 各商品で1日当たりの出荷量を毎日更新する。
が挙げられます。これを現場の生産計画を立てる製造管理者が確認できる状態にしておきます。さらに、これだけでは読むことが難しい各お客様の特売情報などを販売担当者と生産管理者と情報共有してムラに対する準備をおこないます。
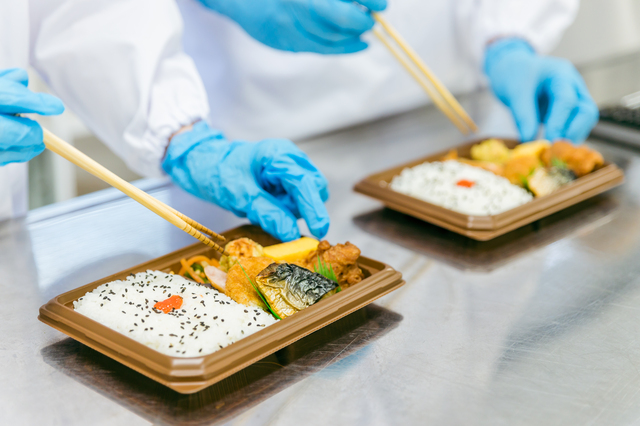
製造部門での「ムラ」のカイゼン
食品はほかの産業と異なり、衛生やアレルギーのコンタミの問題があり製造の立上げ&立ち下げや商品の切り替えに少なくないコストが掛かります。そのため同じ製品を作り続けた方が効率が良いため数日続けて作る、一日の中でも切り替えをしないで作りたい。と考えます。
製造ロットが大きいと、販売予測に修正が有った場合に不良在庫になり賞味期限切れ、または商品は欠品して残業しているのに、原料は賞味期限切れという事が起こります。
このムラのカイゼンには立上げ&立下げと切り替え時間の短縮をおこない、小ロット多品種生産への体制づくりが必要となります。
市場のニーズに対応するためには多能工の育成が必須ですが、同じ作業を続けるような人員配置の方が育成も楽で、単能工にしてしまいがちです。すると製造見込みが外れた場合に対応できる人が少なくて、ある部門は忙しい・暇というようにアンバランスが生まれ生産性、対応力を落としてしまいます。また、作業員も慣れた仕事を好み不慣れな仕事を嫌遠します。そのため多能工に対する人事考課的な評価を上げる、高く評価するという仕組みが必要になり、これを実行するには経営判断によるトップダウンによるカイゼンが必要になります。
ムリ・ムダ・ムラの削減による効果
ムリ、ムダ、ムラを削減し「必要な物を、必要な時に、必要な分だけ作る」ジャストインタイムができるような体制になると生産性が向上するだけでなく、3Kのうちキケン・キツイは解消されていきます。繁忙期と閑散期の休みの差が縮小(完全になくすのは難しいですが)して長期疲労を貯めず働く人の余暇を充実できます。仕事が属人化せず作業者が休みたい時に休みやすくなります。食品は利益率が低いため多くの給料を支払うという事は難しいかもしれませんが、生産性の向上と労働環境・条件の向上は両立させることが可能なのです。
おわりに
いかがだったでしょうか?食品関連産業はインフラ産業的な要素もあり低賃金、厳しい労働条件である産業です。一方で生産性を製造業全体の平均を比べると60%程度しかないとされており、お金を掛けなくても向上の余地はまだまだあります。生産性の向上は労働強化ではなく相反するものです。3Mを削減し生産性を向上させ、従業員のウェルビーイングも向上させる両立は十分可能だと考えています。
コメント